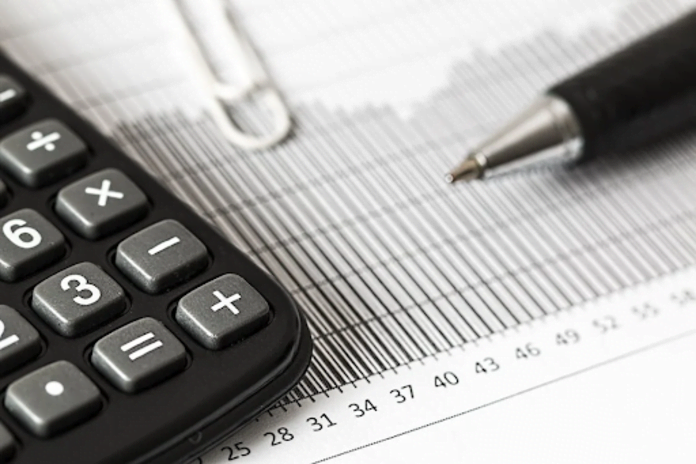
Last year, Shell achieved a significant milestone by scaling its predictive maintenance program to monitor over 10,000 critical equipment pieces. With a technical infrastructure capable of processing 20 billion rows of data weekly from 3 million sensors, today, Shell can use nearly 11,000 machine-learning models to generate 15 million daily predictions. Its managers now remain aware of equipment degradation and other concerns before they can lead to emergency equipment shutdowns.
This global implementation by Shell has garnered praise for its not just economic, but also environmental, and safety benefits. The oil giant now plans to expand the program and explore additional applications of the AI-based Suite, including asset integrity, production optimization, and sustainability.
Experiences such as this make a statement that by embracing technology, organizations can unlock a world of benefits that not only address traditional challenges in maintenance but also pave the way for improved financial outcomes.
Technology in Action: From Preventing Costs To Creating Revenue-Generation Opportunities in Maintenance
Implementing technology to buttress your maintenance function is a proactive approach and brings a major positive change to it.
Illustrating Through Our Own Experience
Let’s delve into an experience with our own solution, where we assisted a specialty maintenance service provider. It partnered with FieldCircle to overcome challenges in maintenance planning along with issues around spare management and transparency.
FieldCircle’s implementation allowed it to manage the entire service lifecycle on one platform, resulting in improved efficiency, real-time visibility, and streamlined documentation.
The collaboration led to a 14% increase in customer satisfaction, a 22% improvement in team productivity, and a 17% rise in asset maintenance contract renewals. As a result, the company could successfully transform its maintenance operations with FieldCircle’s innovative solution.
There’s No Dearth of Success Stories
Moving to another real-life example, we have Bombardier’s success story. The global aviation leader has come up with a ‘Smart Link Plus’ program that empowers aircraft operators with real-time diagnostic data to optimize fleet efficiency, cut maintenance costs, and minimize downtime.
The cloud-based health management program, initially introduced for the Global 7500, is now extended to other new-build Globals and Challengers, with retrofit options available. A Smart Link Plus box collects flight data and transmits it in real-time via in-flight internet and cellular network.
Operators access the data through Bombardier’s maintenance app, thereby enhancing the capabilities of operations and maintenance departments. During this process, privacy and security get equal priority, as data sharing takes place based on user consent. Smart Link Plus has revolutionized the entire maintenance approach, ensuring that Bombardier aligns with the FAA’s connected aircraft vision.
The Benefits Are Clear
These two fine examples are good to deduce that by complementing your maintenance processes with technology, you can demonstrate a change and create an opportunity to improve ROI.
As widely-mentioned statistics from A.T. Kerney’s and Industry Week’s survey have revealed that with tools like computerized maintenance management system (CMMS) and enterprise asset management (EAM) 28.3 percent businesses improved overall maintenance productivity, 20.1 percent reported equipment downtime reduction, 19.4 percent saved on material costs, and 17.8 percent optimized inventory. These statistics are good to repose your trust in technology for enhancing maintenance efficiency.
Overall, technology offers immense potential to revolutionize the maintenance industry, offering invaluable solutions to mitigate financial challenges. The way equipment maintenance software utilization is gaining ground, for instance, bears testimony to this fact. By forecasting equipment failures, equipment maintenance tools keep you abreast of possibilities and arm you with the capabilities to take proactive actions. As a result, the cost of downtime comes down.
By leveraging advanced analytics and machine learning algorithms, maintenance teams can monitor asset health in real time, and detecting anomalies can proactively address potential issues before they escalate into long-term problems. In many ways, the initiative generates savings opportunities, because it reduces downtime (enhancing equipment utilization), and prevents catastrophic failures.
Take for instance a simple use case highlighting the efficacy of CMMS implementation. By integrating a CMMS for your maintenance process, you can feed historical data into an analytics program and derive crucial patterns and trends around key areas like energy consumption. Another notable CMMS feature is audit management. With a CMMS, your audit processes get a well-defined schedule and following a procedural flow, you ultimately improve your equipment’s health.
Considerations for Implementing Technology in Maintenance
While the advantages of technology integration in the maintenance department are compelling, organizations must consider several factors before implementation. The factors include maintenance needs, integration and compatibility of the technology, scalability, training requirement, security robustness, ROI potential, vendor reputation, and readiness to improve continuously.
The initial investment required for acquiring and implementing technology solutions may pose a financial barrier. However, it is essential to evaluate this investment in the context of long-term savings and the potential for improved operational efficiency.
When considered carefully, these considerations ensure a smooth transition and maximize the return on investment (ROI) for technology adoption.
Takeaway
Traditionally maintenance professionals have relied upon tools such as statistical process control (SPC) charts. They have used spreadsheets to keep track of KPIs. With the growing magnitude of maintenance, these are no longer good enough.
Today, a maintenance process generates massive data volumes. The quantity of data is driven by increases in business size, and the variety of device types that come from sensor data from equipment and workstations.
In the face of ongoing changes, custom maintenance management software can give you the edge and make your maintenance operation reach new standards. In any case, technological implementations will be worthwhile investments in maintenance. The sooner you adopt them, the sooner you will start realizing financial benefits.
Featured Image: Fieldcircle
Read more investing news on PressReach.com.Subscribe to the PressReach RSS feeds:- Featured News RSS feed
- Investing News RSS feed
- Daily Press Releases RSS feed
- Trading Tips RSS feed
- Investing Videos RSS feed
Follow PressReach on Twitter
Follow PressReach on TikTok
Follow PressReach on Instagram
Subscribe to us on Youtube